Own a classic car or thinking about getting one? Join us at TOG Hackerspace for a special tinker day dedicated to classic car enthusiasts. It’s a great opportunity to meet fellow owners, share advice, and check out the workshop facilities we have on offer.
This free, open session is all about bringing like-minded people together. While access to group tools like welders and saws is limited to members, we want to give visitors a full tour of the space, chat about what’s possible, and spark ideas for future collaboration.
We don’t have a car lift (yet), but we do have a good selection of gear to support small jobs, including metal car ramps, axle stands, general hand tools, and some specialist equipment, such as a lathe.
Feel free to bring along your classic car and any bits you’re working on. Whether you’re mid-restoration or just want to talk shop, you’re very welcome.
When: Saturday 19th July 2025 from 3 pm to 6 pm
Where: TOG Hackerspace, near the Red Cow, behind Mr Price
Eircode: D12 CF6V – https://www.tog.ie/location
Stick around afterwards for our monthly open social night from 7 pm to 11 pm. We’ll have homemade pizza fresh from our DIY oven and plenty of good company. There’s loads of free parking available on site.
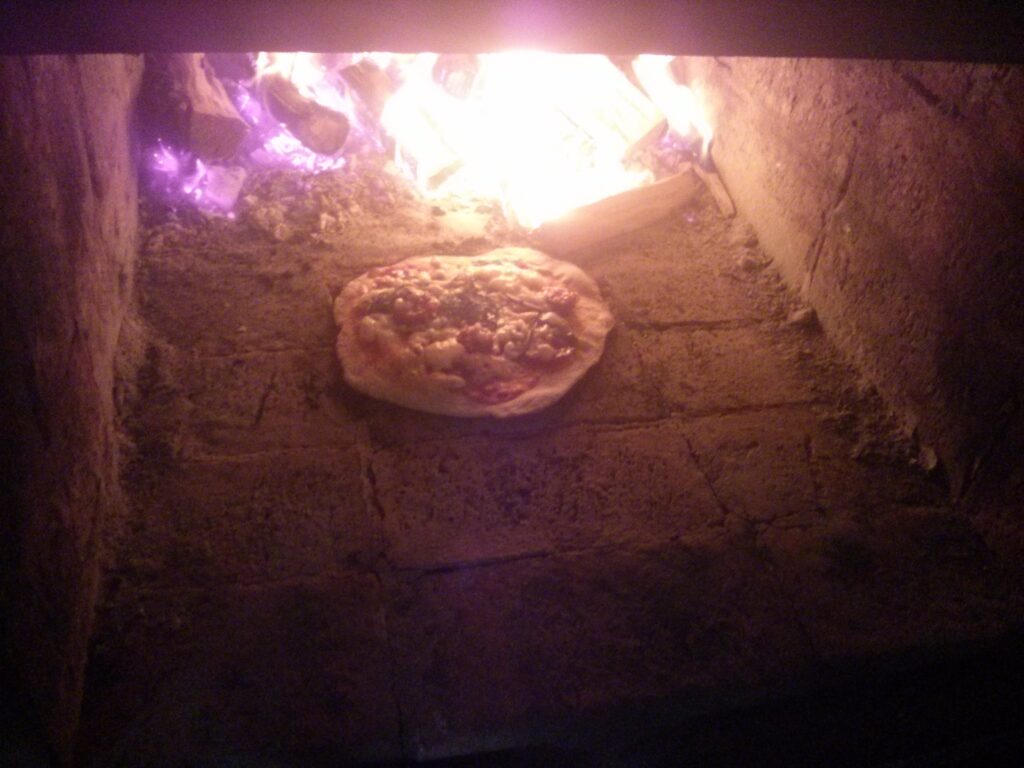
Hope to see you there!